Die casting has become an essential part of Malaysia’s manufacturing industry, playing a crucial role in producing high-quality metal components for various sectors. This advanced manufacturing process involves injecting molten metal into a mold under high pressure, allowing for the creation of precise and durable parts with minimal finishing work required. Over the years, Malaysia has emerged as a key player in die casting, attracting both local and international companies looking for reliable and cost-effective production solutions. With its strategic location, well-developed infrastructure, and skilled workforce, Malaysia continues to strengthen its position as a leading hub for die casting manufacturing. The country’s ability to meet the growing global demand for precision-engineered components has made it a preferred choice for industries looking for high-quality metal casting solutions.
The technological advancements in Malaysia’s die casting industry have significantly contributed to its growth and competitiveness. Many manufacturers have adopted automation and computer-aided design (CAD) systems to enhance precision and efficiency in the production process. Robotics and artificial intelligence are also being integrated into manufacturing plants, reducing human error and improving overall productivity. Additionally, companies are investing in sustainable die casting practices, such as using recyclable materials and energy-efficient processes to minimize environmental impact. These innovations not only improve product quality but also align with global standards, making Malaysian die casting firms more attractive to international clients. With continuous research and development efforts, Malaysia is set to remain at the forefront of die casting technology in the coming years.
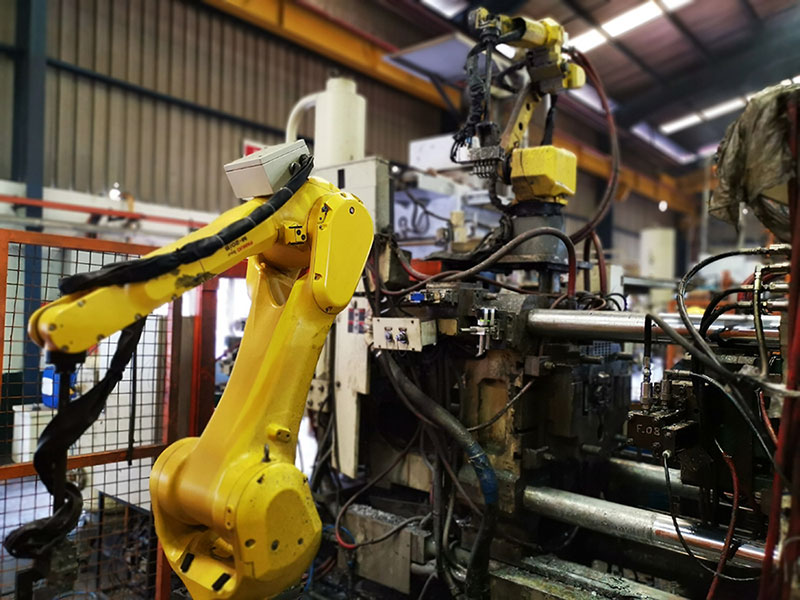
One of the primary industries benefiting from powder coating malaysia capabilities is the automotive sector. Automotive manufacturers rely heavily on die-cast aluminum and zinc components for producing lightweight yet strong vehicle parts. Die-cast engine blocks, transmission housings, and structural components contribute to vehicle performance and fuel efficiency, making them essential in modern car manufacturing. The shift toward electric vehicles (EVs) has further increased the demand for precision die-cast parts, as automakers seek lightweight materials to optimize battery efficiency and overall vehicle weight. Malaysian die casting companies have adapted to these changes by upgrading their facilities and implementing advanced casting techniques to meet the evolving needs of the automotive industry.
Apart from the automotive industry, Malaysia’s die casting sector also plays a significant role in the electronics and consumer goods markets. The electronics industry requires precision-engineered die-cast components for various applications, including smartphones, laptops, and home appliances. These parts provide structural integrity while maintaining a lightweight and compact design, essential for modern electronic devices. Malaysia’s position as a major electronics manufacturing hub has led to a high demand for die-cast components, driving further growth in the industry. Additionally, consumer goods manufacturers benefit from die casting in producing high-quality metal parts for household products, kitchenware, and power tools. The versatility of die casting allows for the production of intricate and durable components that enhance product quality and functionality.
Despite the promising growth of Malaysia’s die casting industry, it faces several challenges that require strategic solutions. The fluctuating costs of raw materials, such as aluminum, zinc, and magnesium, can impact production expenses and profit margins. Additionally, competition from other manufacturing powerhouses, such as China and India, puts pressure on Malaysian firms to maintain their market share. To stay ahead, companies must focus on innovation, quality assurance, and customer service, ensuring that their products meet global industry standards. Government support through research and development grants, workforce training programs, and tax incentives can also help strengthen the industry. By addressing these challenges proactively, Malaysia can continue to expand its die casting sector and attract more investments from international manufacturers.
The future of die casting in Malaysia looks promising, driven by technological advancements and the increasing demand for precision-engineered components. The adoption of Industry 4.0 technologies, including data analytics, machine learning, and IoT-based monitoring systems, is expected to enhance efficiency and streamline production processes. Sustainability will also be a key focus, with manufacturers adopting eco-friendly practices to align with global environmental regulations. As Malaysia continues to position itself as a leader in precision manufacturing, its die casting industry will play a crucial role in supplying high-quality components to a wide range of industries worldwide. With a strong commitment to innovation and excellence, Malaysia is set to remain a dominant force in the global die casting market for years to come.